Quality control of our steel products
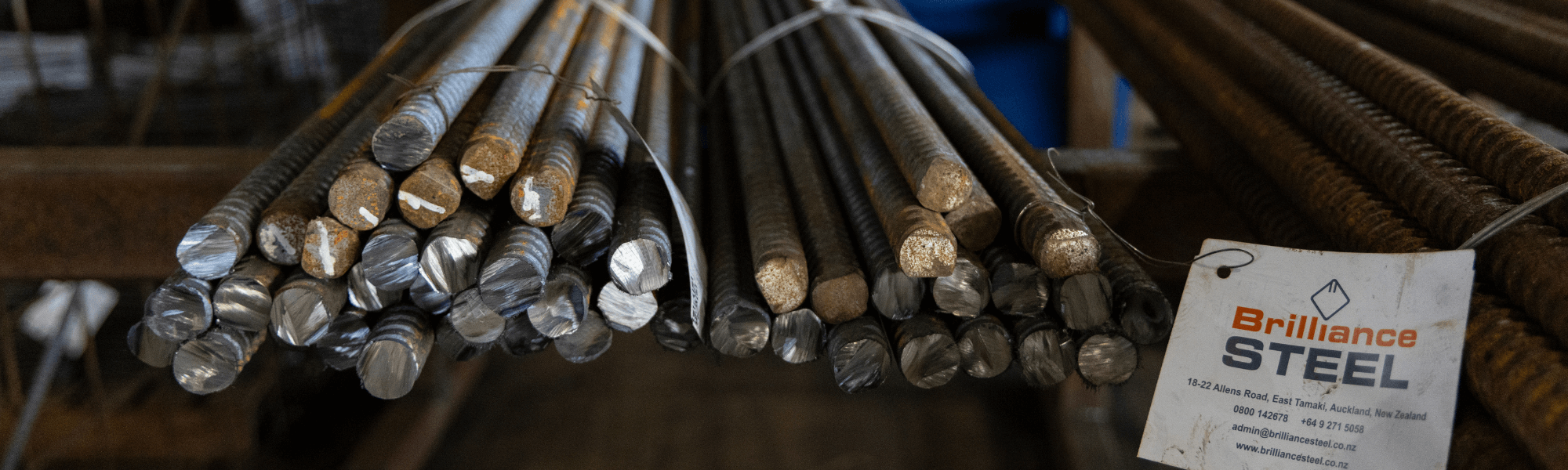
At Brilliance Steel, we take great pride in ensuring our clients receive the highest-quality steel available, thanks to our selective steel sources and rigorous in-house testing in our Auckland manufacturing warehouse.
10,000 to 20,000 tonnes of steel per year is made into Brilliance Steel’s products and we ensure every tonne is sourced from ACRS-approved mills, meeting the strict requirements of the New Zealand Building Code (AS/NZS4671: 2019 Code of Compliance).
How do we ensure our reinforcing steel products are of the highest quality?
If you’re a part of New Zealand’s construction industry, you’ll know how important it is to have top-quality materials.
We start at the source, ensuring the steel mills we work with around the world are ACRS-approved.
In July 2024, we acquired the ACRS Product Conformity Certification - Processing and distribution of carbon steel bars and distribution of mesh. We are the first and currently the only reinforcing steel company in New Zealand to hold this certification.
This certification ensures that our steel processing and product traceability system fully complies with the AS/NZS 4671 standard.
The ACRS Australasian Certification Authority for Reinforcing and Structural Steels is an independent and non-profit organisation that is the leading and most technically rigorous steel certifier to New Zealand and Australian standards.
Our quality management system is ISO 9001 certified, confirming we follow all industry best practice to a world-recognised standard. And we gained the ISO 9001 for approved quality management system.
But we don’t stop there – we also put every batch of steel through rigorous testing in our in-house laboratory.
Our state-of-the-art onsite laboratory puts all our steel through rigorous testing
In 2022, Brilliance Steel invested in its laboratory to add another layer of confidence for our clients.
The Brilliance Steel lab is accredited by IANZ and operated according to the New Zealand compliance requirements of testing and calibration laboratories (ISO 17025:2018).
Our testing capability generates invaluable insights into our products’ performance, allowing us to confirm the material’s strength, flexibility and ability to handle environmental pressures.
We start with visual inspections, ensuring the steel has the required finishes without any discernible defects.
Next, the steel goes through a tensile testing process, giving us thorough insights into how the steel will behave when subjected to extreme tensile forces and environmental pressures.
Our state-of-the-art hydraulic and electromechanical testing equipment allows staff to put the steel through additional pressure testing that examines yield strength, elongation, modulus of elasticity, and fracture behaviour.
This allows Brilliance Steel to provide clients with comprehensive reports on the precise quality of the steel they’ll be using in their engineering and construction projects.
We are happy to extend our laboratory testing to researchers, engineers and any other industries that want to check the quality of their steel. We actively encourage partnerships that can make use of our tools and research.
What are the risks with using untested steel?
While you might be able to spot defects on the surface, the real hazards come from internal flaws that risk the integrity of both the steel, the project and your reputation.
By testing our steel, Brilliance Steel eliminates risk of structural failure at the product level that might lead to collapse once tensile pressures exist. Untested steel poses a significant safety risk to both workers and end users.
Steel that hasn't been tested for quality may corrode or degrade faster than anticipated, resulting in a reduced lifespan, higher maintenance costs, and risk of negative experiences for construction and engineering clients.
You can be confident that Brilliance Steel reinforcing products comply with – and in some cases exceed – all New Zealand standards. This in turn helps ensure your projects are legally compliant, minimising liability. Project managers who are confident in the quality of their steel also don’t need to worry about the significant delays and increased costs caused by the late discovery of deficiencies.
These points highlight the critical importance of thorough quality testing for steel used in engineering and construction.